The first step is the processing of bamboo strips from the bamboo stem
The stem (culm) are cut lengthwise into sections that are split by radial blades into strips. The raw strips are then planed, sanded, and thermally treated against mold and insects. The strips can be additionally “baked” to obtain a darker (“caramelized”) tint. In the end the strips are dried in an oven.
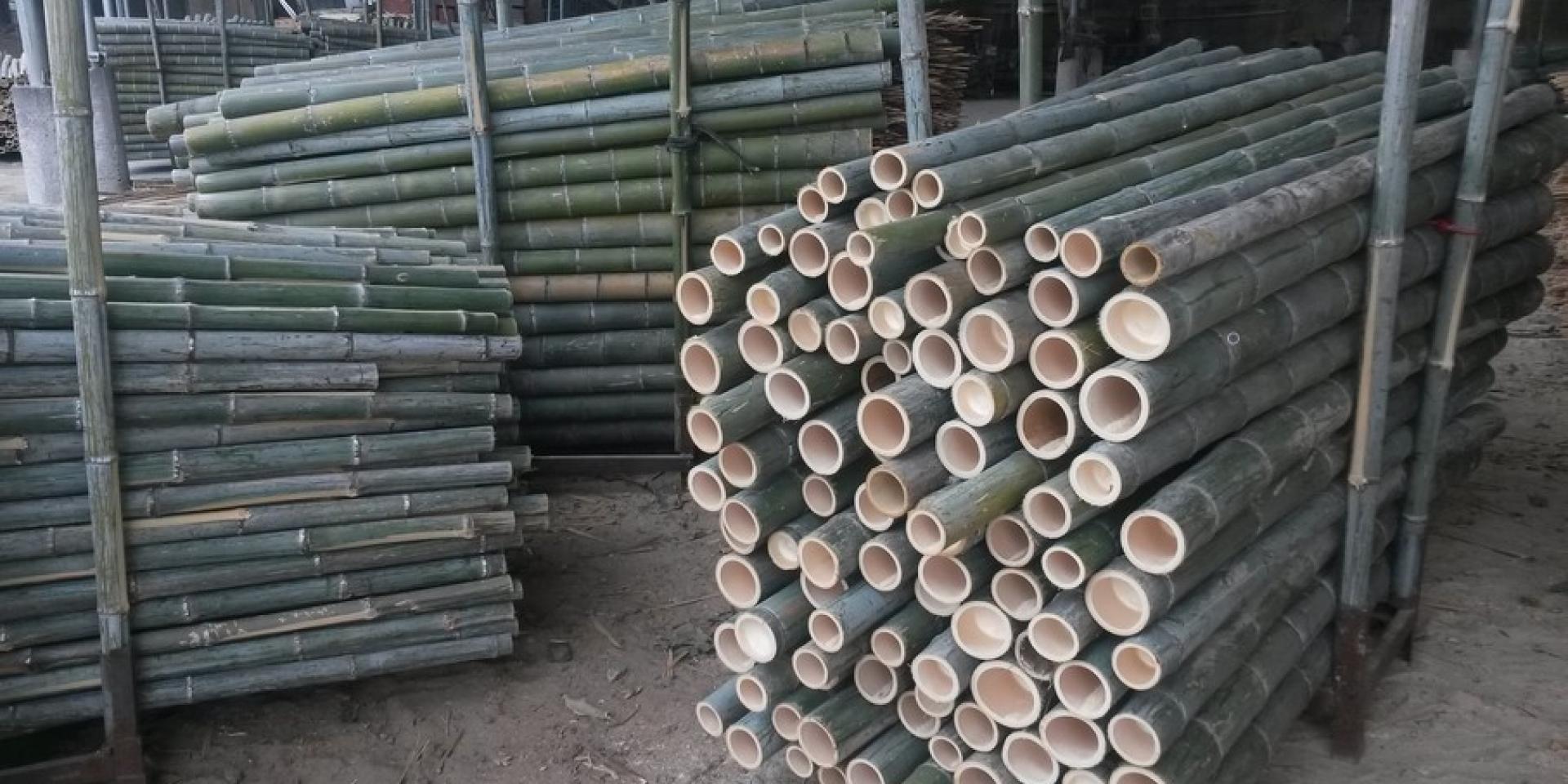
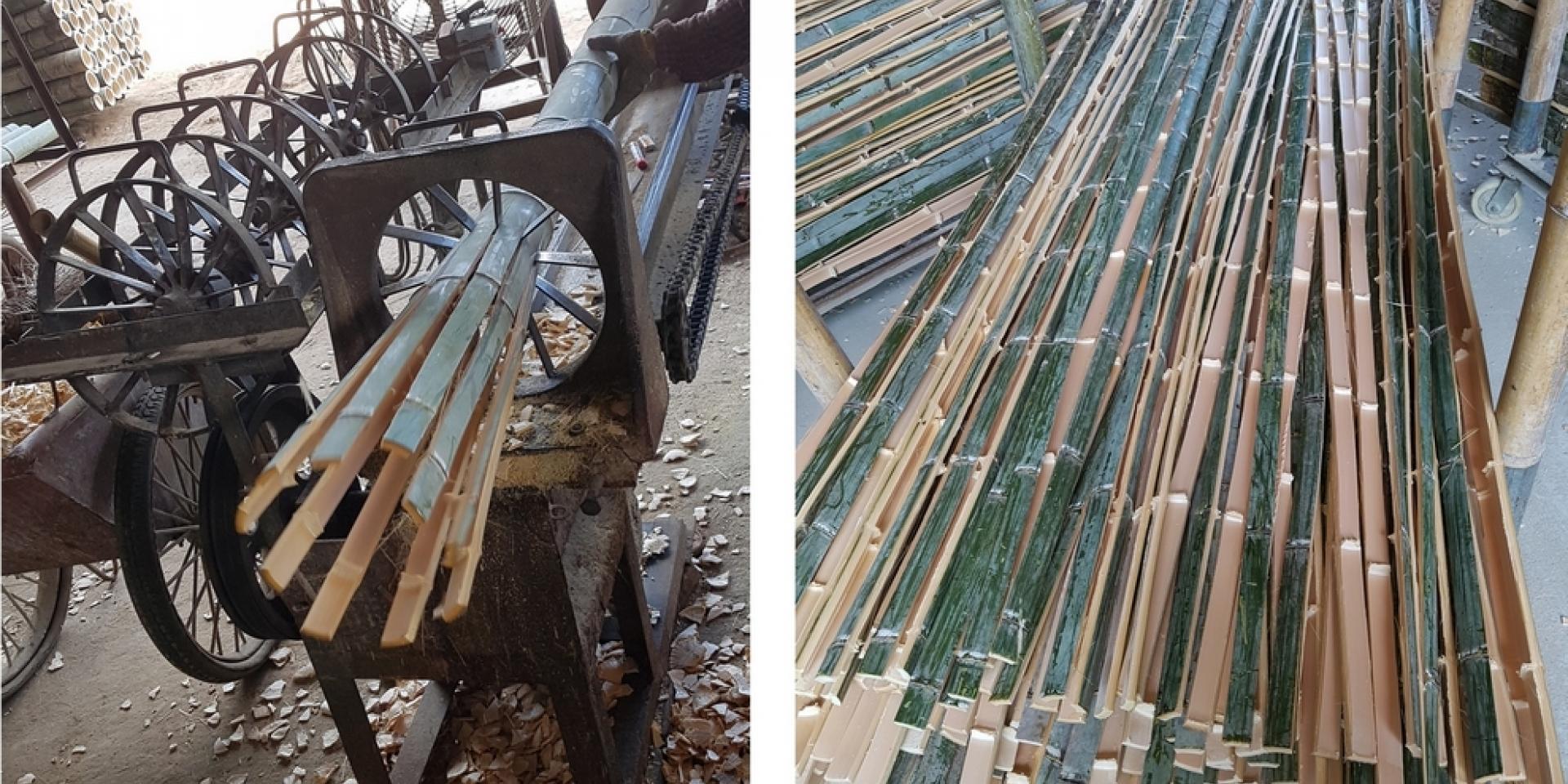

Second step: creation of laminated boards
There are two basic ways of assembling the strips: Horizontally, the strips are pressed and glued on theirs long sides; or vertically, the strips are pressed and glued on their large faces. Those panels can be superimposed, glued, and pressed, to create various types of “sandwiches”. For example, several layers of superimposed horizontal layer to create a thick “horizontal” board; or combination of vertical and horizontal layers to optimize the mechanical and esthetical characteristics of the “sandwich” board.
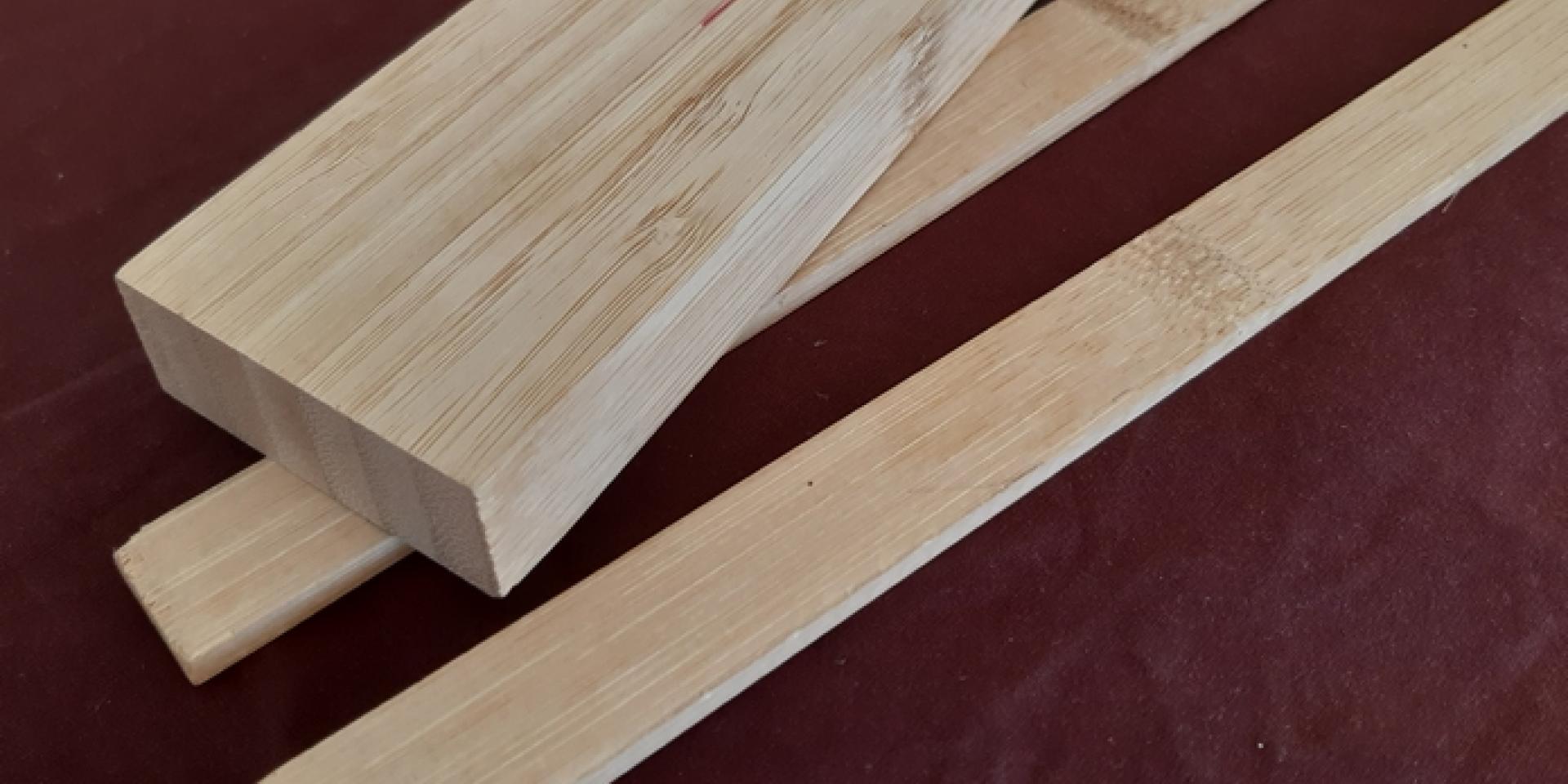
Final step: The fabrication of our bamboo furniture
As we have seen above, the processed bamboo strip is the basic element for the industrial fabrication of bamboo boards (used for furniture, flooring, etc.)
Our line of furniture is fabricated at factories specialized in making large modern bamboo furniture based on bamboo boards. It requires a specialized know-how using specialized computer numerically controlled machines.
The strips are the basic element of our furniture. We also use laminated panels (beams) for the structural elements (frames). The concept, style, of tsimtsum attempts to minimize the material consumption, and the visual and physical space of the furniture (minimalism). We strive to minimize the impact of our furniture on the environment while also minimizing the price for our final consumers.